In hot summer or special working environment, air compressors, as key power equipment, often face many problems such as over-high temperature, reduced operating efficiency, and increased failure rate. If effective measures are not taken in time, it may cause equipment damage or even shutdown, affecting the entire production process. Therefore, formulating and implementing effective high temperature response plans is crucial to ensure the stable operation of air compressors.
Ⅰ. The impact of high temperature on air compressor operation
1. Accelerated deterioration of lubricating oil
High temperature will cause the viscosity of lubricating oil to decrease and the lubrication performance to weaken, which will affect the operation of the core components of the air compressor, and in severe cases may cause the main engine to jam.
2. Reduced heat dissipation efficiency
When the ambient temperature is too high, the load of the cooling system increases, and poor heat dissipation will cause the temperature rise of the whole machine to accelerate, increasing the risk of shutdown protection.
3. Overheating of the electrical system
High temperature can easily cause overheating of the control cabinet and motor, causing problems such as line aging and electrical failure.
4. Decreased air quality
High temperature weather is often accompanied by increased humidity, and the moisture in the intake air increases, which can easily cause water rust and blockage in the back-end gas-using equipment.
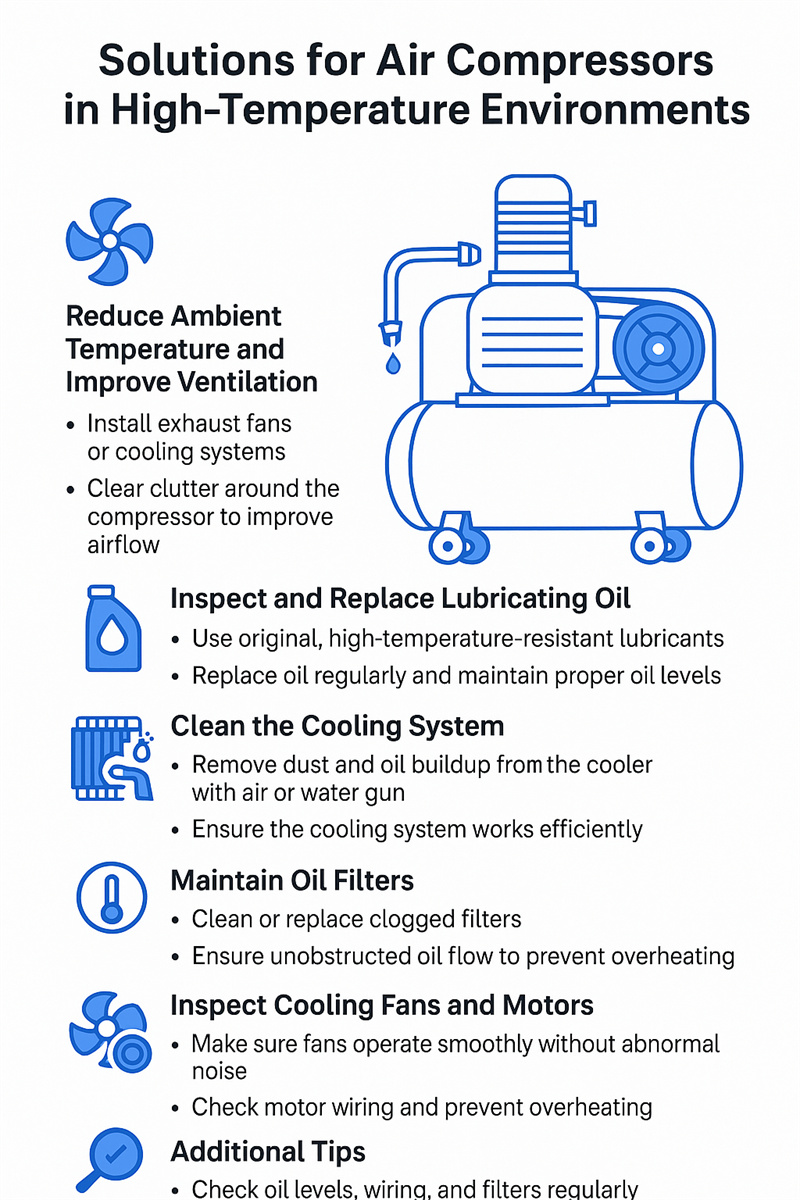
Ⅱ. High temperature solution for air compressor
1. Improve the installation environment
Maintain good ventilation: Ensure smooth air circulation in the air compressor room, and install a powerful exhaust fan or air conditioning system to cool down if necessary.
Stay away from heat sources: Avoid air compressors near high-heat equipment such as boilers and furnaces to reduce heat radiation interference.
2. Optimize the cooling system
Cleaning the radiator: Regularly clean the dust and oil on the surface of the oil cooler and air-cooled radiator to improve the heat exchange efficiency.
Check the coolant status (such as water-cooled models): Check the water quality and circulation status of the cooling water to avoid scale accumulation or water pump failure.
3. Strengthen lubrication management
Select lubricating oil with excellent high temperature performance: It is recommended to choose a special air compressor oil with good thermal stability and antioxidant properties.
Regular oil change: Regularly check the oil level and color of the lubricating oil and replace it in time.
4. Electrical system protection
Check the fan and motor: Ensure that the fan speed is normal, the motor has no abnormal sound, and there is no sign of overheating.
Strengthen the ventilation of the electrical cabinet: A cooling fan or air conditioner can be installed to keep the control system temperature stable.
5. Intelligent monitoring and early warning
Install intelligent monitoring modules to monitor key parameters such as temperature, pressure, and operating status in real time, provide early warning, and reduce the risk of sudden failures.
III. Summer operation and maintenance suggestions
1. Reasonably arrange the operation time: avoid the high temperature period at noon, and staggered operation can effectively reduce the load.
2. Increase the inspection frequency: check the key parts such as oil level, exhaust temperature, and cooling effect every day to find hidden dangers in time.
3. Train operators: Improve the high temperature emergency handling ability and maintenance awareness of front-line employees.
IV. Conclusion
High temperature poses a severe test to the stable operation of air compressors, but through scientific and reasonable management and maintenance measures, various faults caused by high temperature can be effectively prevented, ensuring the long-term stable operation of equipment and escorting the continuous production of enterprises.
Post time: May-12-2025