Laser chillers are key components to ensure stable operation of laser equipment, and their performance directly affects the output power and service life of lasers. If daily maintenance is not in place, it may lead to reduced heat dissipation efficiency, frequent equipment failures, and even damage to the core components of the laser. Therefore, mastering scientific maintenance methods is the basis for ensuring long-term stable and efficient operation of the laser system.
1. Cooling water replacement: the primary task of maintenance
Cooling water is prone to breed microorganisms, form scale and impurities during the circulation process, and then block the waterway or corrode internal components. To avoid these problems, it is recommended:
-Replacement cycle: Replace cooling water every 3 to 6 months.
-Water quality requirements: Use deionized water, pure water or special coolant, and avoid using ordinary tap water.
-Replacement process: Completely drain the old water, clean the water tank and pipes, and then inject new water to ensure clean water quality.
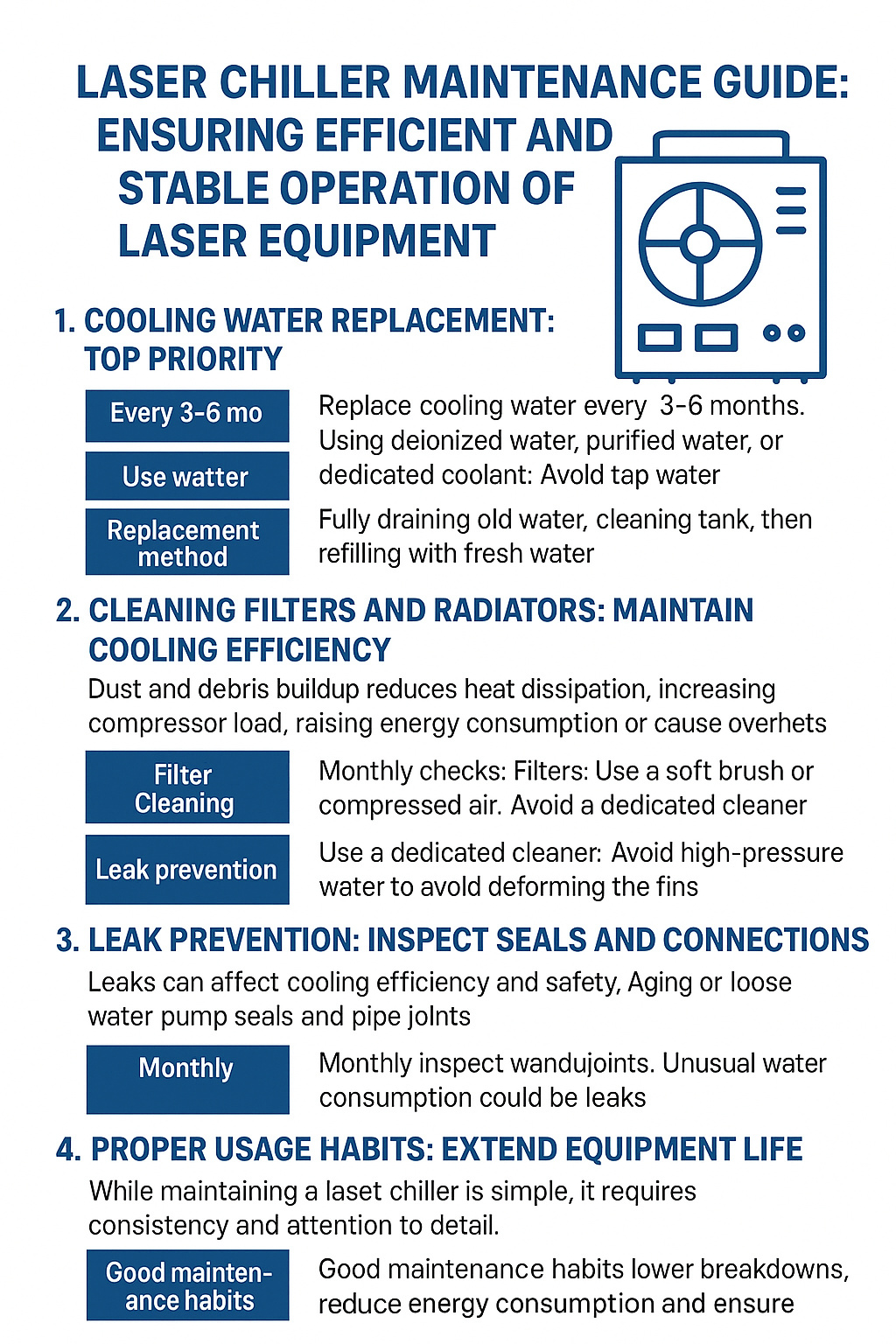
2. Cleaning the cooling system: ensuring cooling efficiency
Dust and debris accumulated on the filter and radiator will seriously affect the heat dissipation effect, increase the load of the compressor, increase energy consumption, and even shut down due to overheating. The following operations should be performed regularly:
—Filter cleaning: Check once a month and clean the dust with a soft brush or compressed air.
—Radiator cleaning: Use special cleaning agents to clean the fins regularly, avoid direct impact with high-pressure water, and prevent deformation and damage.
3. Waterway sealing inspection: Prevent hidden dangers of water leakage
After long-term operation, the water pump, water pipe joints and other parts may age and loosen, resulting in water leakage, which not only affects the cooling efficiency, but also may endanger the safety of the laser.
—Inspection frequency: Check the water pump seal ring, joints, etc. for water leakage every month.
—Abnormal handling: If the cooling water consumption is found to be abnormally accelerated, the system should be fully checked for leaks in a timely manner, and the aging accessories should be replaced.
4. Operation status monitoring: Early warning of potential faults
By monitoring the various operating parameters of the chiller, problems can be discovered in advance to avoid sudden faults:
—Monitoring content: Whether the water temperature, water pressure, flow, alarm information, etc. are within the set range.
—Data fluctuations: If abnormal fluctuations in parameters are found, the machine should be stopped immediately for inspection to prevent the expansion of the fault.
5. Reasonable use habits: extend equipment life
-Avoid frequent start and stop: Frequent start will accelerate the wear of the compressor. When the laser equipment is temporarily out of service, the chiller can be kept running at a low speed.
-Long-term shutdown treatment: If long-term shutdown is required, the water circuit should be completely drained to prevent low-temperature freezing and pipeline rupture.
6. Summary
Maintaining a laser chiller is not complicated. The key lies in "regular inspection, meticulous operation and standardized use". Good maintenance habits can not only significantly extend the service life of the chiller and laser, but also reduce energy consumption and failure rate, providing a solid guarantee for the efficient operation of the laser processing system.
If you need a laser chiller maintenance record sheet, operation manual or chiller selection recommendations that match your company's equipment, you can also contact me at any time.
Post time: May-19-2025